Solder Paste
Low Ag
PW233-ST355-GQ-4
0.3Ag Composition Solder Paste
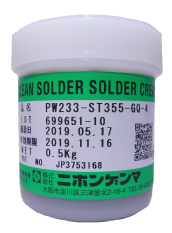
Excellent Stability of Viscosity under Hot and Humid Environment
Excellent Continuous Printing Performance while Adding Paste
Test Result of Continuous Printing under High Temperature and Humidity
Able to use even under hot and humid environment with minimal change of viscosity.
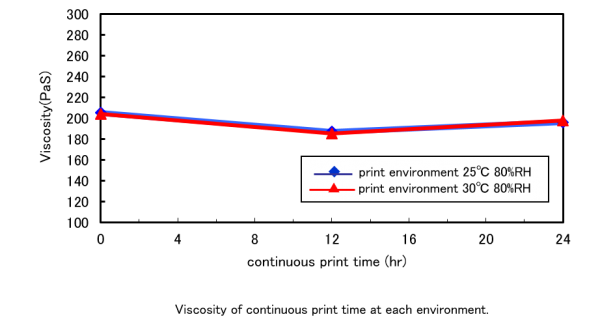
Test Result of Continuous Printing while Adding Paste
When printing while adding paste, there is almost no deterioration in properties even after 7 days of use.
Printing Condition
Squeegee: Metal Type, Angle 60°, Width 280mm
Squeegee Stroke: 25cm
Printing Speed: 30mm/ sec
Printing Pressure: 22 x 10-2N
Interval: 30sec
Environment: Temperature 26°C~28°C Humidity 30%~50%
Place a 500g of solder paste on the stencil, 250g solder paste from the machine will replace with new solder paste after 4 hours. Collect the remaining solder paste after 8 hour printing and keep it in the refrigerator for 16 hours. This process will repeat for 7 days.
Viscosity of Adding Solder Paste while Printing for 7 days
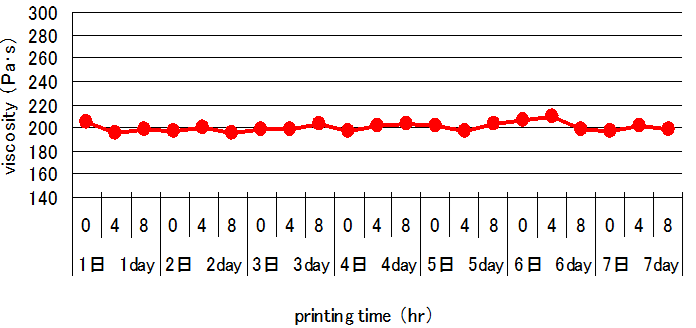
1st day
|
7th day
|
||
Printability (0.4mm pitch QFP)
|
|
|
![]() |
Melting (0.4mm pitch QFP) |
![]() |
![]() |
The Solder Paste Condition after Printing for 7 Days (Excellent) |
Characteristics PW233-ST355-GQ-4
|
||||
Alloy Composition
|
Sn-0.3Ag-3.0Bi-0.5Cu
|
![]() |
||
Melting Point
|
207℃~224℃
|
♦ Low Ag |
||
Powder Type
|
Type4
|
♦ Ensuring Strength while Reducing Cost | ||
Halide Content |
0.02wt%±0.01 |
![]() |